- Blog
- /
Automated Packaging Solutions: Eliminating Manual Operations with Septimatech
Jan 27, 2025
Modern packaging lines require more than just speed—they require flexibility, accuracy, and minimal downtime during changeovers to meet customer and consumer demand expectations are met.
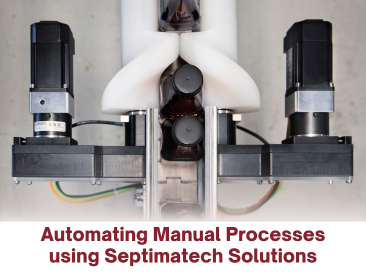
Septimatech's automated solutions, including Feed Screws/Timing Screws, Downed Bottle Reject Systems, and Adjustable Guide Rails, and Bottle Inverters address and automate operational challenges. In this blog, we explore how these 3 specific solutions we provide can be used to automate manual tasks on packaging lines.
1. Feed screws: Enhancing Precision and Reducing Manual Labor on lines.
An important process on packaging lines is controlling the spacing and orientation of containers. On smaller lines, these processes are often done manually, resulting in limited output speeds. This is because performing these tasks manually can be time-intensive and opens the door to human error, particularly for operations handling a wide range of container shapes and sizes. Septimatech’s feed screws / timing screw solutions eliminate these challenges by providing:
- Precision Handling: Feed screws ensure consistent spacing and positioning of containers, reducing errors and preventing misfeeds that could jam downstream equipment.
- Faster Changeovers: With Septimatech's solutions, feed screws can be quickly changed out to handle multiple container formats without needing lengthy manual recalibration. This reduces downtime and increases overall throughput.
- Safety and Ergonomics: Automation removes the need for operators to manually reposition or adjust containers, eliminating repetitive strain injuries and enabling operators to focus on other, higher-value add tasks.
By automating manual processes with feedscrews...
manufacturers can gain significant improvements in control and speed, especially for industries like food, beverage, and pharmaceuticals, where accuracy and hygiene are critical.
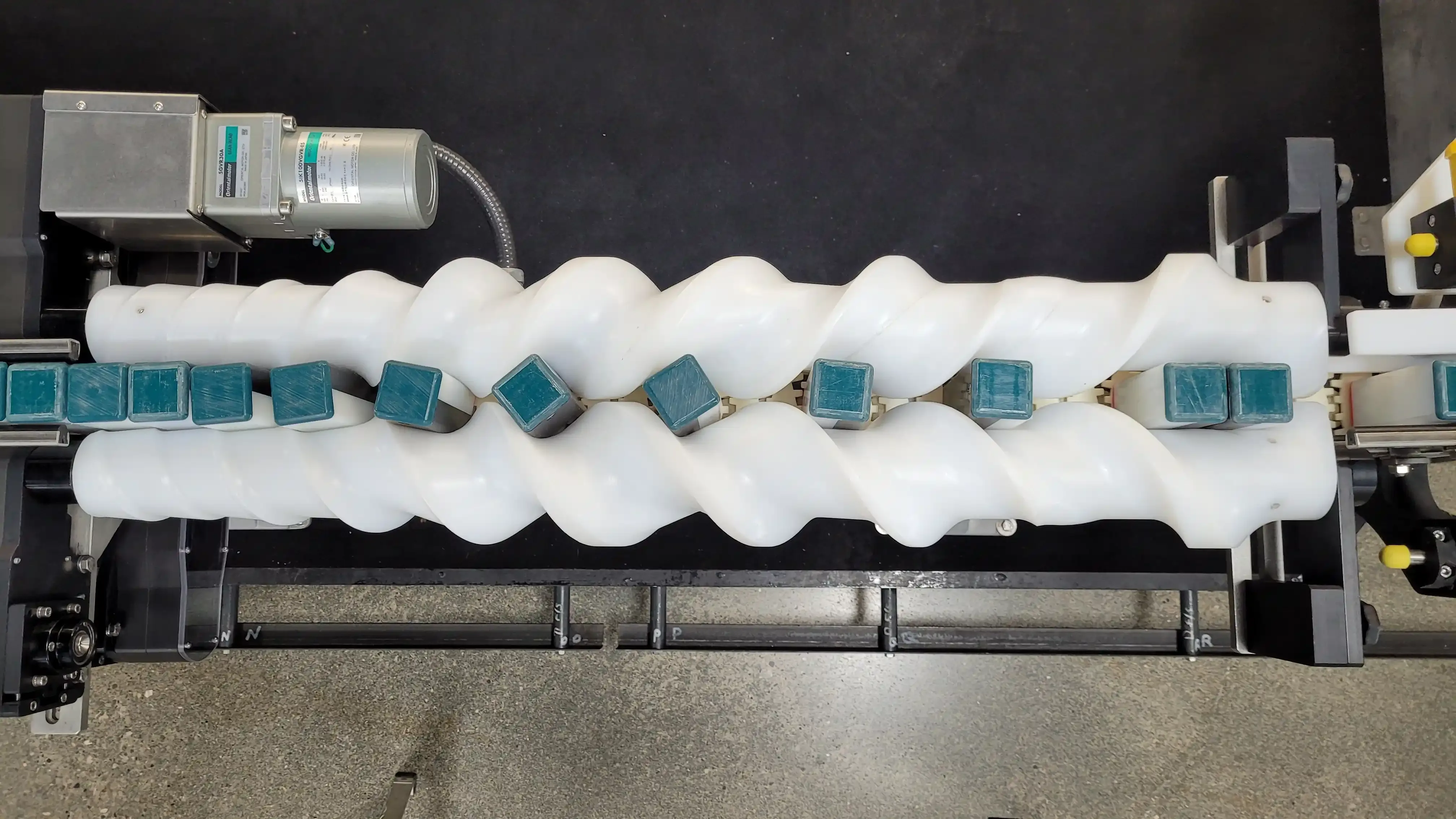
2. Downed Bottle Reject Systems: Reducing Crashes
Having an operator spend time to identify and remove fallen bottles can slow operations, result in errors leading to crashes, and elevate labor costs. Septimatech’s downed bottle reject systems automate this process through a simple mechanical system. They can provide the following benefits:
- Uninterrupted Production Flow: Bottles that are fallen, or improperly positioned can be automatically removed without halting the line maintaining production efficiency.
- Improved Quality Control: “Automated” removal of downed bottles removes the element of human error. It ensures higher accuracy than manual inspections, ensuring no containers enter an area of the line in an incorrect position or orientation.
- Labor Optimization: Operators don’t need to stop production to remove downed products manually, freeing them to focus on other tasks and minimizing the need for additional labor during peak operations.
By integrating downed bottle reject systems into packaging lines...
manufacturers can reduce the amount of crashes that occur due to fallen bottles and improve worker productivity.
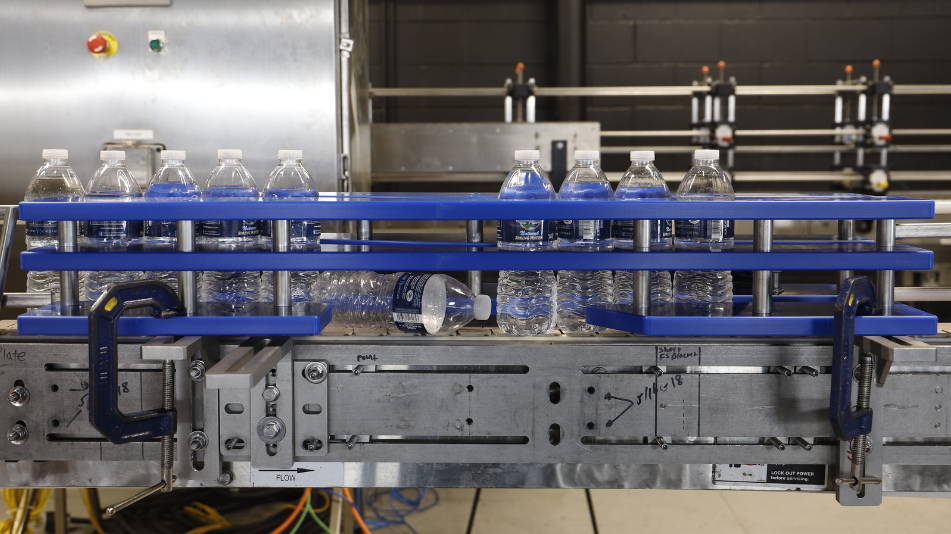
3. Adjustable Guide Rails: Streamlined Changeovers for Maximum Productivity
Adjustable guide rails make accommodating a variety of product sizes and shapes on a single packaging line easy. However, manual adjustments are not only time-consuming but also can be prone to incorrect line setups between changeovers. Septimatech’s EASY Adjust Rails eliminate these issues by:
- Fast, Repeatable Adjustments: Operators can quickly changeover a whole line with little effort from minimal adjustment locations. This allows for more frequent product changeovers with very little downtime.
- Consistency Across Runs: Automated systems ensure precise, repeatable changeovers that eliminate human error and variation between operators. This reduces the risk of alignment issues that can slow down production or damage products.
- Supporting Sustainability: By optimizing guide rail adjustments and reducing waste from improperly handled containers, Septimatech’s solutions align with sustainability goals.
Septimatech’s Adjustable Guide Rail Solutions…
combine ease-of-use, speed, and precision, making them perfect for facilities that have frequent changeovers between bottle formats.
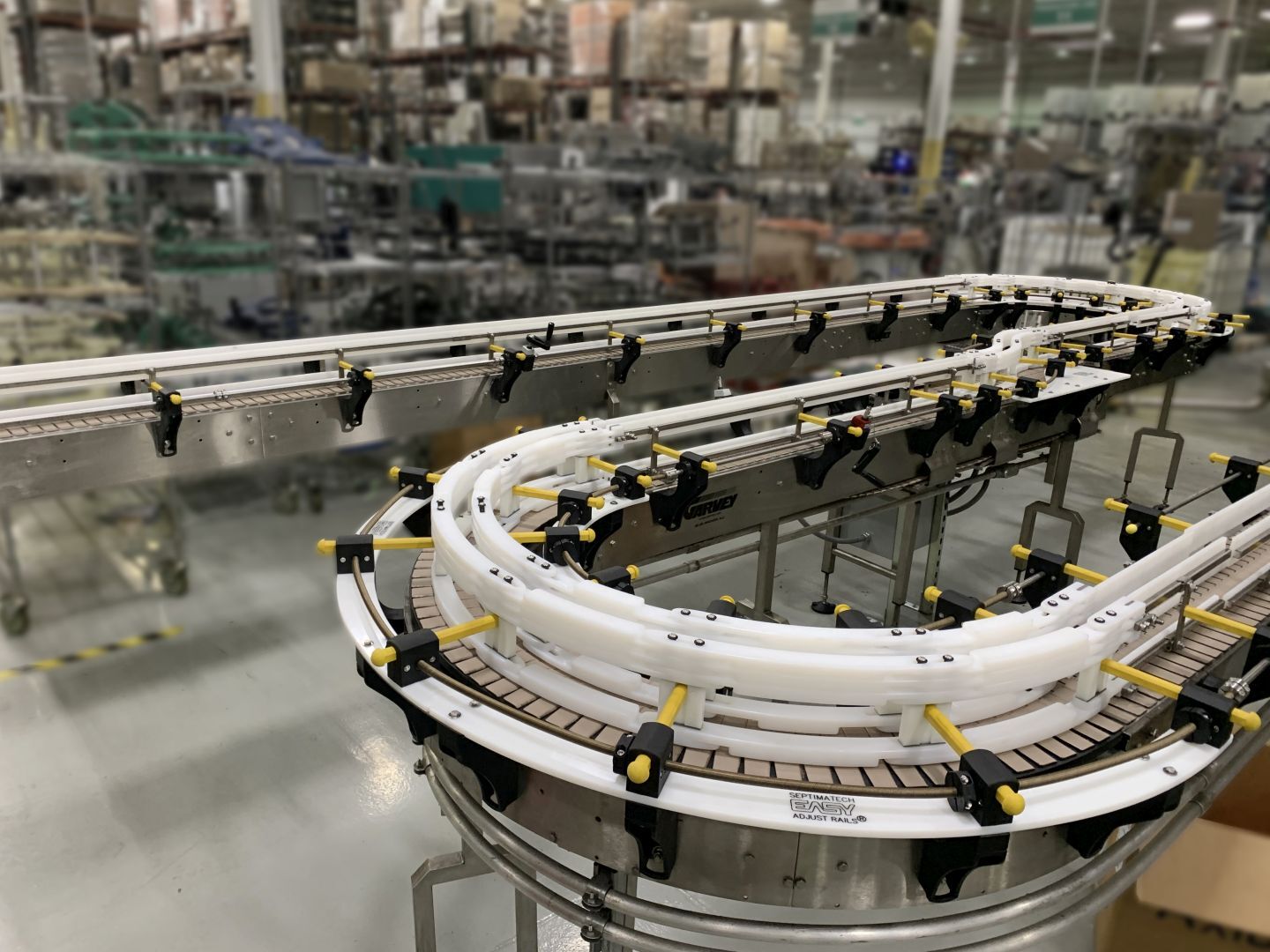
4. Bottle Inverter Solutions: Container Orientation Made Easy
Bottles often go through some kind of inverting process on a packaging line. This could be for a number of reasons - blowing out the bottle with ionized air, labelling, sealing the lid etc... but these processes are often challenged by the limits of manual labor. Septimatech’s bottle inverter solution eliminates these challenges by providing:
- Consistent Orientation: Septimatech's Bottle inverter design ensures that each individual bottle passes through the bottle twist at exactly the same orientation.
- Faster Changeovers: With Septimatech's inverters, different size formats can quickly changed out without needing any manual recalibration.
- Touch-free inversions: The bottle inverter completely eliminates the need for an operator to touch the bottle.
Inverting and orienting using a Bottle Inverter...
ensures that your operators will not be prone to repetitive strain injuries, all while improving your throughput.
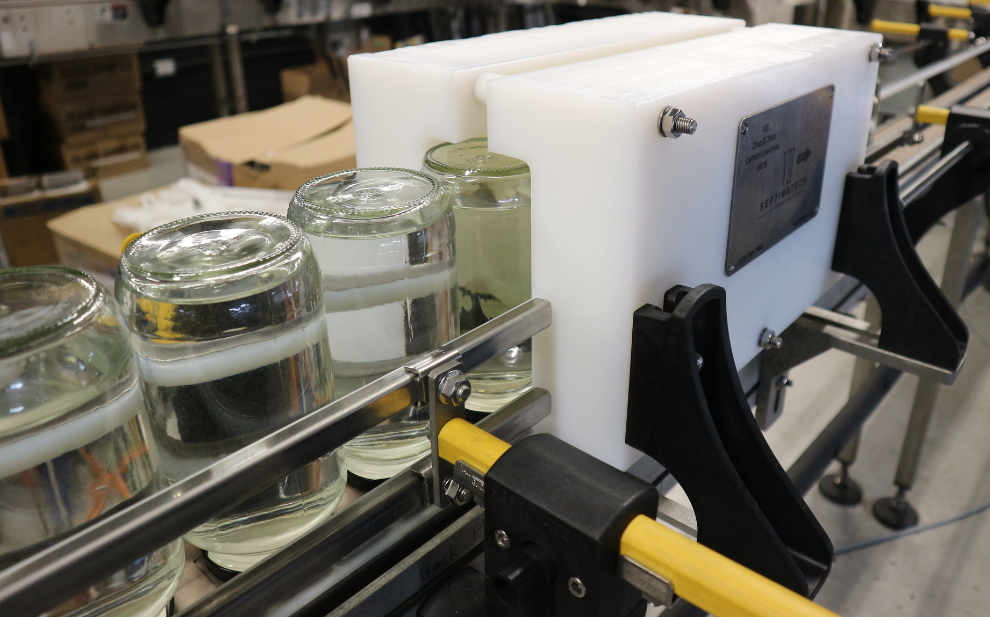
Why Do Septimatech Solutions Stand Out?
Septimatech’s approach to automation emphasizes user-friendly design, alongside reliability and reliability. By eliminating manual processes our solutions allow packaging lines to:
- Reduce labor costs by automating routine tasks.
- Maximize uptime with faster changeovers and fewer disruptions.
- Enhance operator safety by reducing physical strain and repetitive motions.